In the world of industrial operations, equipment reliability is a cornerstone of productivity and efficiency. The significance of systematic overhaul and maintenance of industrial equipment cannot be overstated. This comprehensive guide will delve into the best practices that ensure the longevity and optimal performance of your machinery.
Understanding Industrial Equipment Overhaul  Â
Industrial equipment overhaul is a detailed and intricate process that involves a thorough inspection, disassembly, cleaning, repair, and reassembly of machinery to restore it to its optimal working condition. This process is essential for prolonging the lifespan of equipment and preventing unexpected breakdowns that could disrupt operations.
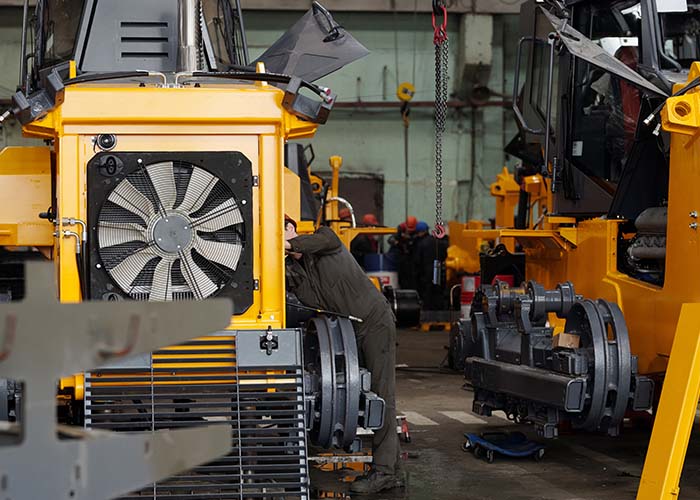
Importance of Regular Overhaul Â
Regularly overhauling industrial equipment helps in:
Minimizing Downtime: Scheduled overhauls prevent unexpected equipment failures, reducing operational downtime.
Enhancing Safety: Well-maintained equipment is less likely to fail, ensuring a safer working environment.
Cost Efficiency: Preventive maintenance is generally less expensive than emergency repairs and replacement.
Optimal Performance: Regular overhauls ensure that equipment functions at peak efficiency, improving productivity.
Why You Need Industrial Equipment Overhaul  Â
Maintaining the operational integrity of industrial equipment is crucial for several reasons:
1. Ensuring Operational Efficiency: Equipment that operates efficiently uses less energy and performs tasks more quickly and accurately. Over time, components wear out, leading to decreased performance and higher energy consumption. Overhauling equipment restores it to like-new condition, ensuring it operates at maximum efficiency.
2. Extending Equipment Lifespan: Industrial equipment represents a significant investment. Regular overhauls extend the usable life of machinery, delaying the need for costly replacements. This proactive approach to maintenance ensures you get the most out of your investment.
3. Reducing Unplanned Downtime: Unexpected equipment failures can halt production, leading to costly downtime. Regular overhauls identify and address potential issues before they result in breakdowns, keeping your operations running smoothly and avoiding unplanned stoppages.
4. Enhancing Workplace Safety: Malfunctioning equipment poses safety risks to workers. Regular overhauls ensure that all safety features are functioning correctly and that the equipment is in good working order, thereby reducing the risk of accidents and injuries in the workplace.
5. Compliance with Regulations: Many industries are subject to strict regulatory requirements regarding equipment maintenance. Regular overhauls help ensure compliance with these regulations, avoiding fines and ensuring that your operations meet industry standards.
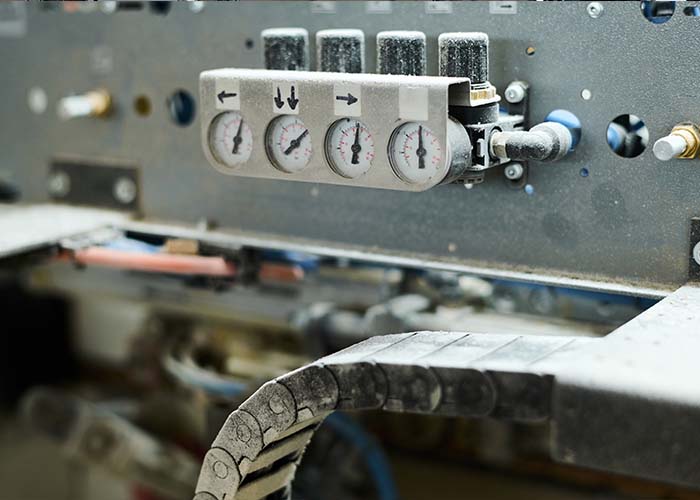
Best Practices for Industrial Equipment Maintenance  Â
Maintenance is a continuous process that complements overhauls. Implementing a robust maintenance strategy is key to the longevity and efficiency of industrial equipment.
1. Preventive Maintenance Â
Preventive maintenance involves regular, scheduled inspections and servicing of equipment to prevent unexpected failures. This includes:
Routine Checks: Regularly inspecting critical components such as bearings, belts, and motors.
Lubrication: Ensuring that all moving parts are adequately lubricated to reduce friction and wear.
Calibration: Periodically calibrating equipment to maintain accuracy and performance.
2. Predictive Maintenance Â
Predictive maintenance utilizes advanced monitoring techniques to predict when equipment failures might occur. This proactive approach includes:
Vibration Analysis: Monitoring vibrations to detect misalignments or imbalances.
Thermography: Using thermal imaging to identify overheating components.
Oil Analysis: Analyzing lubricants for contaminants and wear particles.
3. Corrective Maintenance Â
Corrective maintenance is carried out after a fault is detected. While it is more reactive, it is essential for addressing issues that are not covered by preventive or predictive maintenance. This includes:
Minor Repairs: Fixing issues such as leaks or minor mechanical failures immediately.
Major Repairs: Conducting more extensive repairs during planned downtime to minimize disruption.
4. Documentation and Record Keeping Â
Keeping detailed records of all maintenance activities is crucial. This helps in:
Tracking Maintenance History: Understanding the equipment’s maintenance history for better decision-making.
Planning Future Maintenance: Scheduling future maintenance activities based on past performance and issues.
Compliance: Ensuring compliance with industry regulations and standards.
Implementing a Maintenance Management System  Â
A robust Maintenance Management System (MMS) can significantly enhance the effectiveness of your maintenance strategy. An MMS helps in:
Automating Scheduling: Automatically scheduling maintenance activities based on equipment usage and performance data.
Resource Management: Managing inventory of spare parts and allocation of skilled technicians.
Performance Monitoring: Continuously monitoring equipment performance and generating reports for analysis.
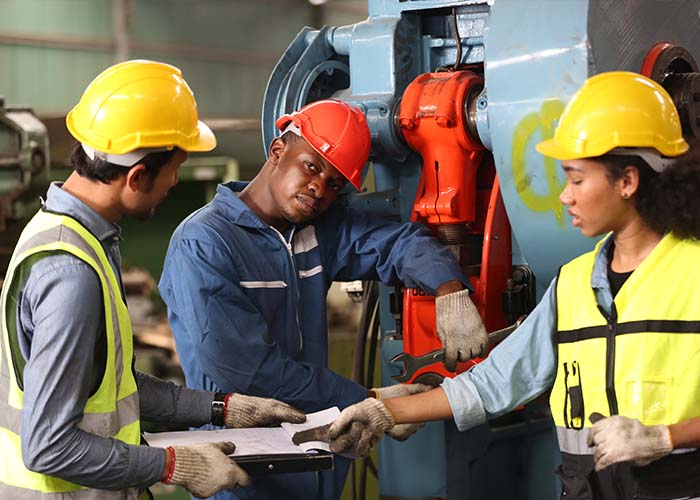
Training and Development  Â
Investing in the training and development of maintenance personnel is vital. This includes:
Technical Training: Ensuring technicians are skilled in the latest maintenance techniques and technologies.
Safety Training: Providing regular safety training to prevent accidents and injuries.
Ongoing Education: Encouraging continuous learning and certification in relevant fields.
Conclusion  Â
Adopting best practices for industrial equipment overhaul and maintenance is essential for maximizing the lifespan, reliability, and performance of your machinery. By implementing a comprehensive maintenance strategy that includes preventive, predictive, and corrective maintenance, supported by a robust Maintenance Management System and skilled personnel, you can ensure the smooth and efficient operation of your industrial equipment Â