Introduction
An efficiently optimized conveyor system is crucial to the success of any manufacturing or logistics operation. Whether in assembly lines or warehouse automation, maintaining a steady flow of materials and products can dramatically enhance productivity, reduce costs, and ensure operational success.
However, inefficiencies in conveyor systems can cause bottlenecks, downtime, and increased operational costs.In this guide, we delve into key strategies for optimizing conveyor systems, focusing on improving efficiency and minimizing disruptions. Whether your goal is to boost throughput, lower energy consumption, or extend your system’s lifespan, this comprehensive guide provides practical tips to elevate performance.
Understanding Conveyor System Efficiency
Conveyor system efficiency hinges on multiple factors, such as speed, reliability, energy use, and the system’s ability to manage varying loads without interruptions. When a conveyor system is poorly maintained or inadequately designed, operational inefficiencies arise.
These issues may result in unexpected breakdowns, prolonged downtime, higher energy expenses, inconsistent material handling, and even safety risks.
To overcome these challenges, businesses must adopt targeted optimization techniques that enhance performance and streamline operations.
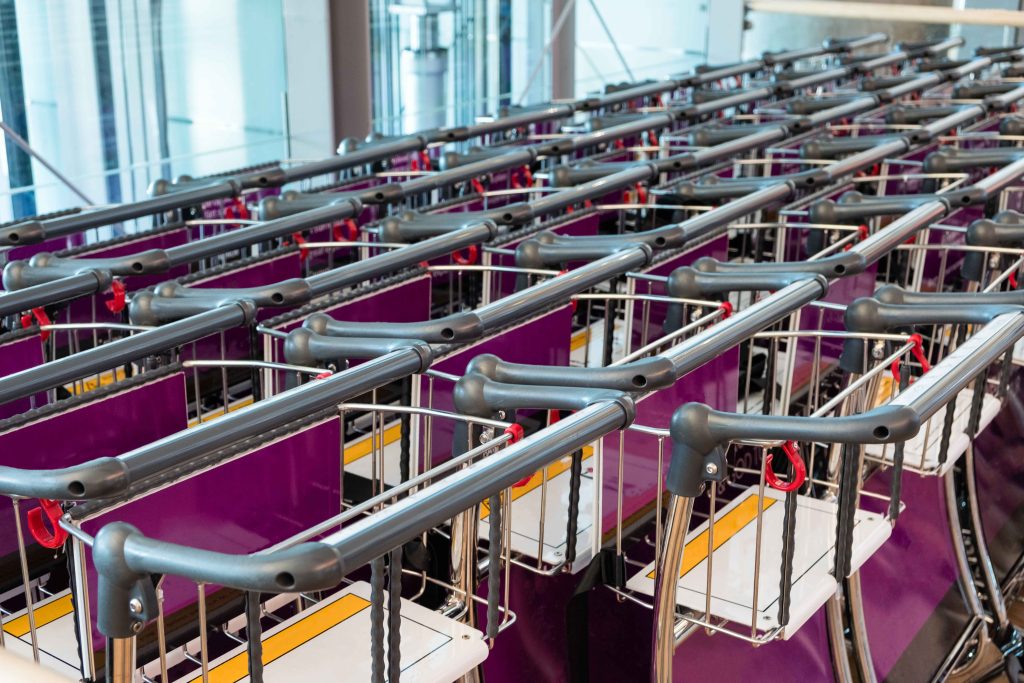
Key Strategies to Enhance Conveyor System Performance
1. Regular Maintenance and Inspections: Preventive maintenance is essential to reduce unplanned downtime and extend the life of conveyor system components. A well-structured maintenance schedule should include the following practices: ensuring moving parts are properly lubricated to minimize wear, checking belt tension and alignment to prevent misalignment and slippage, inspecting critical components (such as rollers, bearings, and motors) to detect early signs of wear, and conducting routine cleaning and debris removal to prevent slowdowns and potential damage.
2. Adjusting Conveyor Belt Speed: Proper belt speed is fundamental to maintaining an efficient workflow. When setting belt speeds, consider production demands, material handling requirements, and energy efficiency.
Production needs often require adjusting speeds to align with output levels, while material handling considerations ensure that items are moved at an appropriate pace to prevent damage. Excessive speeds can lead to unnecessary energy consumption and higher operational costs, so striking the right balance is crucial.
3. Reducing Bottlenecks and Optimizing Layout: Bottlenecks are significant barriers to productivity. Analyzing and refining the conveyor system layout can help eliminate flow restrictions. Strategic placement of conveyors ensures smooth transitions between different stages of the process.
Additionally, incorporating smart automation, such as sensors, can help regulate material flow and prevent overloads. Implementing buffer zones in the system also provides temporary storage, reducing the risk of bottlenecks and maintaining a continuous operation.
4. Upgrading to Advanced Conveyor Technologies: Integrating modern technology into your conveyor system can significantly improve efficiency. IoT-enabled sensors offer real-time monitoring of system performance and can alert operators to potential issues before they lead to failures. Using Variable Frequency Drives (VFDs) enables precise control over conveyor speed, optimizing energy use.
Additionally, AI-driven predictive maintenance systems leverage data analytics to identify and resolve potential failures before they occur, reducing both downtime and maintenance costs.
5. Enhancing Energy Efficiency: Reducing power consumption is key to managing operational costs. Switching to energy-efficient motors minimizes overall energy use. Smart control systems that automate the start-stop functions ensure that the conveyor operates only when necessary. Furthermore, regenerative drives can capture and reuse energy generated by braking processes, further enhancing the system’s energy efficiency and reducing operational costs.
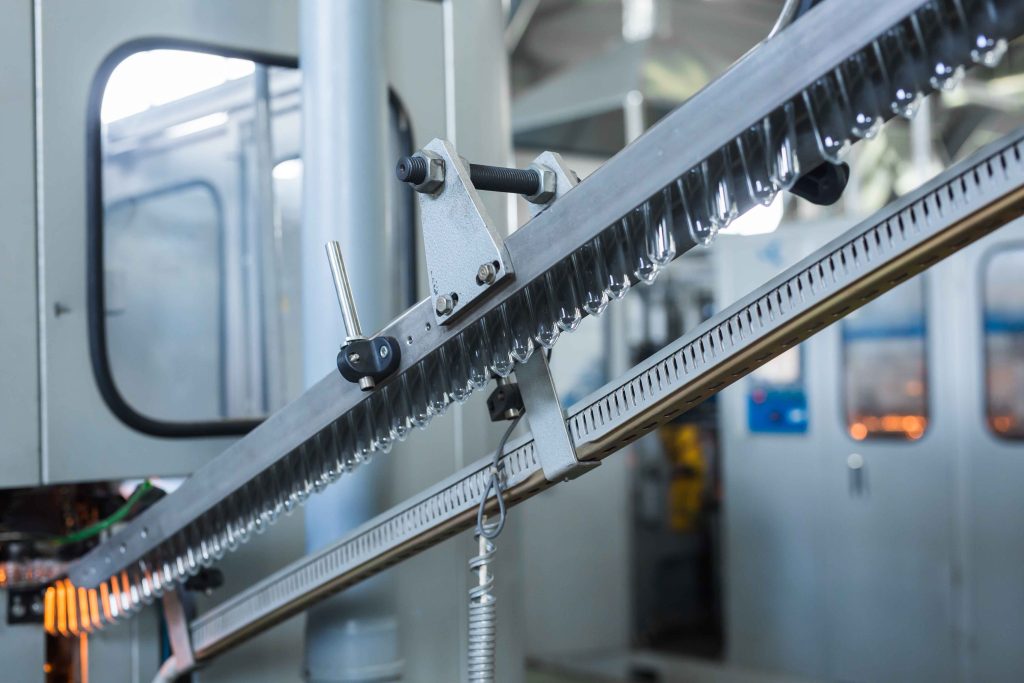
Real-World Results of Conveyor System Optimization
A large manufacturing company faced ongoing challenges with conveyor system inefficiencies, leading to frequent downtime, production delays, and increasing costs. Issues such as excessive wear on components, inconsistent belt speeds, and lack of real-time monitoring were disrupting operations and driving up energy consumption.
To address these challenges, the company adopted a comprehensive conveyor optimization strategy. Key changes included implementing a preventive maintenance program to regularly inspect, lubricate, and replace worn parts before they failed. Conveyor speed settings were adjusted according to production needs, reducing energy consumption while maintaining a steady flow of materials.
The company also incorporated automation and IoT-enabled sensors to monitor real-time performance and make adjustments dynamically.
As a result, the company saw a 30% increase in throughput, enabling them to meet production targets more efficiently. The adjusted speed settings and reduced idle time led to a 25% reduction in energy consumption, significantly cutting operational costs.
Moreover, the proactive maintenance and integration of smart technology reduced unplanned breakdowns, lowering maintenance expenses.
This case demonstrates the substantial impact of strategic conveyor system enhancements in improving both productivity and profitability.
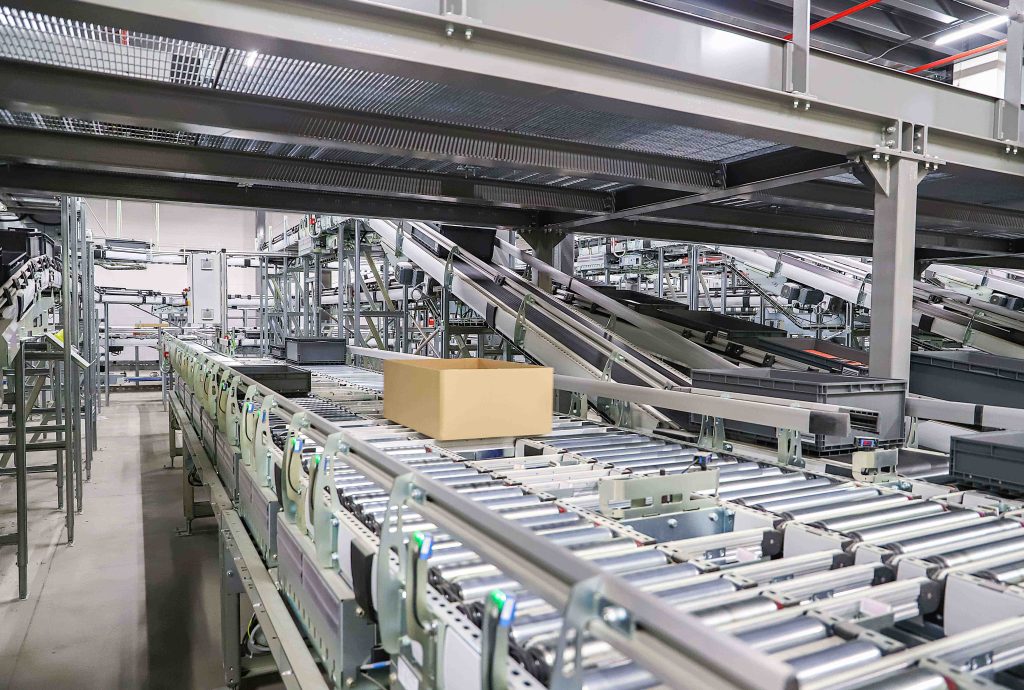
Conclusion
Optimizing your conveyor system involves more than just routine maintenance. It requires implementing strategic improvements that enhance productivity, reduce costs, and create smoother, more efficient operations. Whether through automation, layout optimization, or energy-saving technologies, each adjustment contributes to a more streamlined workflow.
Is your conveyor system running at peak efficiency? Start by assessing your current setup, identifying inefficiencies, and applying these proven strategies to elevate your system’s performance.
Looking to optimize your conveyor system?
Reach out to us today for a free assessment and discover how our expert solutions can enhance your operations and maximize productivity.